Sibelco is a global material solutions company, specialised in mining, processing, and selling industrial minerals. Headquartered in Antwerp, Sibelco operates over 100 production sites in more than 30 countries across the globe. Focusing on silica, clays, feldspathics, and olivine, Sibelco’s provides material solutions across a broad range of industries. With environmental and social responsibility at the core of its vision, strategy and day-to-day business, Sibelco is dedicated to be a frontrunner when it comes to sustainable operations.
Sibelco’s Clay Press Operations
Sibelco’s plant in Cornwood mines kaolin clay, a type of clay used primarily in ceramics, sanitaryware and engineered stone. After mining, the moist clay is not yet ready for further processing, the excess moisture must first be squeezed out of the clay. This is done using a clay press so that the optimum moisture content is achieved for its further applications.
The clay pressing process can be divided into three phases. In the first phase, the clay pres is filled with moist clay. Subsequently, the most clay is squeezed to remove water. Lastly, in the third phase, the clay is dropped out of the press. The duration of each of these three phases influences three important aspects of the clay pressing process:
- Throughput: the faster the clay pressing process, the higher the throughput will be
- Quality: if the clay pressing process is taking too long or too short, the quality of the clay may be affected, as the residual moisture level can be either too low or too high.
- Energy use: the clay pressing process requires a significant amount of energy. If the process is taking longer, more energy is used.
Improving the Status Quo
Sibelco’s average throughput per hour at that time was approaching the maximum capacity of the clay press, hence only small improvements (approximately 5%) could potentially be realised. However, a small improvement in throughput per hour eventually materialises to a significant additional yield and revenue per year. Moreover, if improvements could be realised, a roll-out to other plants across the globe would definitely would make the business case worth it.
Sibelco was dedicated to find a reliable partner that would be able to develop a data-driven optimisation tool for improving the throughput of the clay pressing process. Faktion’s expertise in process optimisation, and more specifically yield and throughput optimisation, proved to be the perfect match for a strategic partnership.
Quantifying the Relationship Between Filling Time and Throughput
To optimise clay press throughput, Faktion built an AI-based optimisation dashboard, allowing to simulate different strategies and providing insights into the outcomes of these simulations. To come up with this AI-based optimisation dashboard, several steps were taken.
An exploratory data analysis revealed that the squeezing and dropping phases in the clay pressing process were quite rigid and, if executed according to the predetermined setpoints, there was little room for improvement. The press filling phase was more interesting. The efficiency of the filling process decreases over time, since the volume in the clay press is limited. Resistance to the filling increases over time as it becomes progressively harder to add extra clay to the press that is started to become full, comparable with trying to putting a sleeping bag back in its cover. Moreover, the press filling process is powered by pumps that consume a significant amount of energy, which implied that potential energy savings could be realized next to throughput improvements.
Mathematically, the press filling process follows an exponential decay function, as indicated by the figure below. The filling time can be seen as a predetermined period of time that clay will be added to the press, no matter how full the press is. The clay mass in the press keeps increasing as long as clay is added to the press (indicated by filling time), although at a progressively slower rate (decay), until a ceiling (maximum press capacity) is hit.
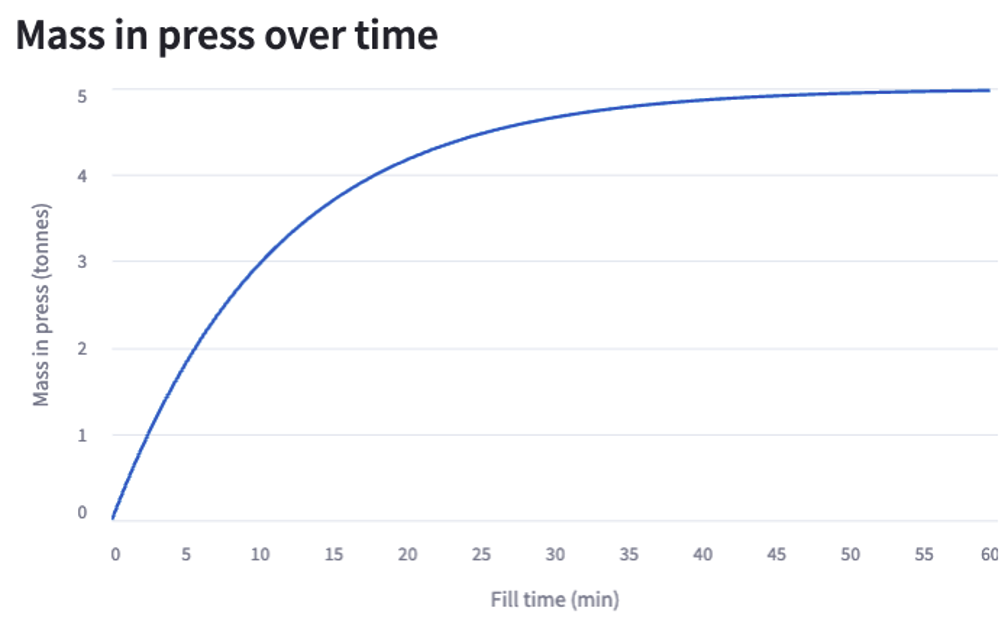
The fact that the clay press filling process follows an exponential decay function implies that, after a certain optimal filling time, the throughput will decrease with longer filling times. After all, if the clay mass in the press increases at a progressively slower rate as filling times get longer, proportionally speaking, less clay can be pressed as filling time increases, leading to a decrease in throughput, as indicated by the figure below. A simple calculation might simplify this reasoning. Suppose that the squeezing and dropping phase together take 45 minutes. Based on the visual above, we can say that if the fill time is fixed at 15 minutes, approximately 3.5 tonnes of clay will be added to the press. Together with the squeezing and dropping phase, his implies a throughput of 3.5 tonnes per hour. On the other hand, if the filling time is fixed at 60 minutes, approximately 5 tonnes of clay can be added to the press. This results in a throughput of approximately 2.9 tonnes per hour. Hence, after a certain optimal filling time, throughput starts decreasing. But how can we find this optimal filling time?
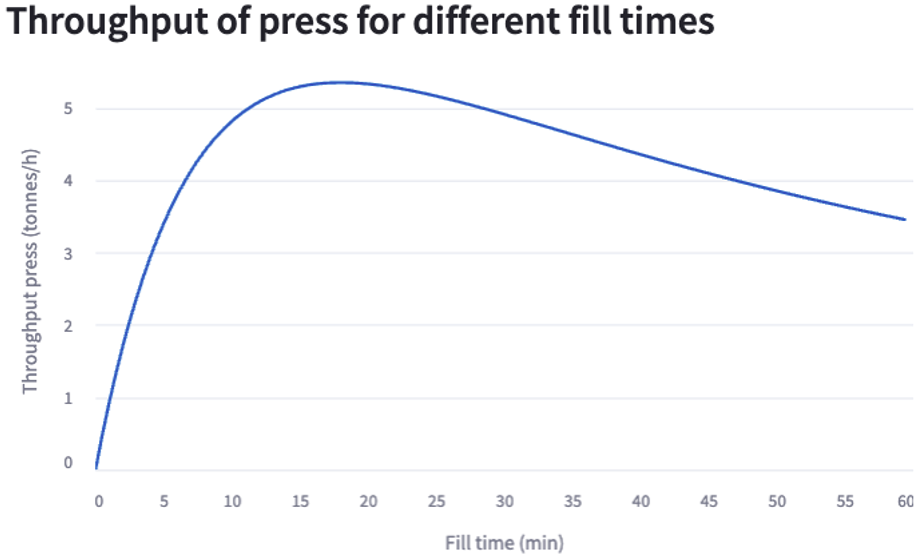
The Result? A Significant Reduction in Energy Use
These insights were used in a simulation model within the optimisation dashboard. The dashboard not only allows to inspect descriptive statistics of press process characteristics like filling time or throughput, but also to examine specific pressing cycles and deep dive on specific periods or devices. Besides the data exploration and visualisation, a valuable feature was added to determine the optimal filling time. After specifying some adjustable process parameters, such as clay type, clay density, and clay temperature, the optimal filling time is derived through simulation and the associated throughput and filling pump energy are calculated, as well as a comparison with the average ‘as-is’ press filling strategy. From the simulations, we found that after optimisation of the filling time, the throughput was expected to increase by 5% on average. While this throughput increase is seems small, the energy reduction was expected to be more significant. From the simulation, optimising the filling time is expected to reduce the filling pump energy use by 12%. Besides these results, a potential malfunction in one of the presses was detected. If repaired, the throughput might be increased and energy use might be reduced even further. As a next step in this project, Faktion and Sibelco are planning to move the full data pipeline to a cloud environment, allowing to extend this analysis to other presses and locations within Sibelco.